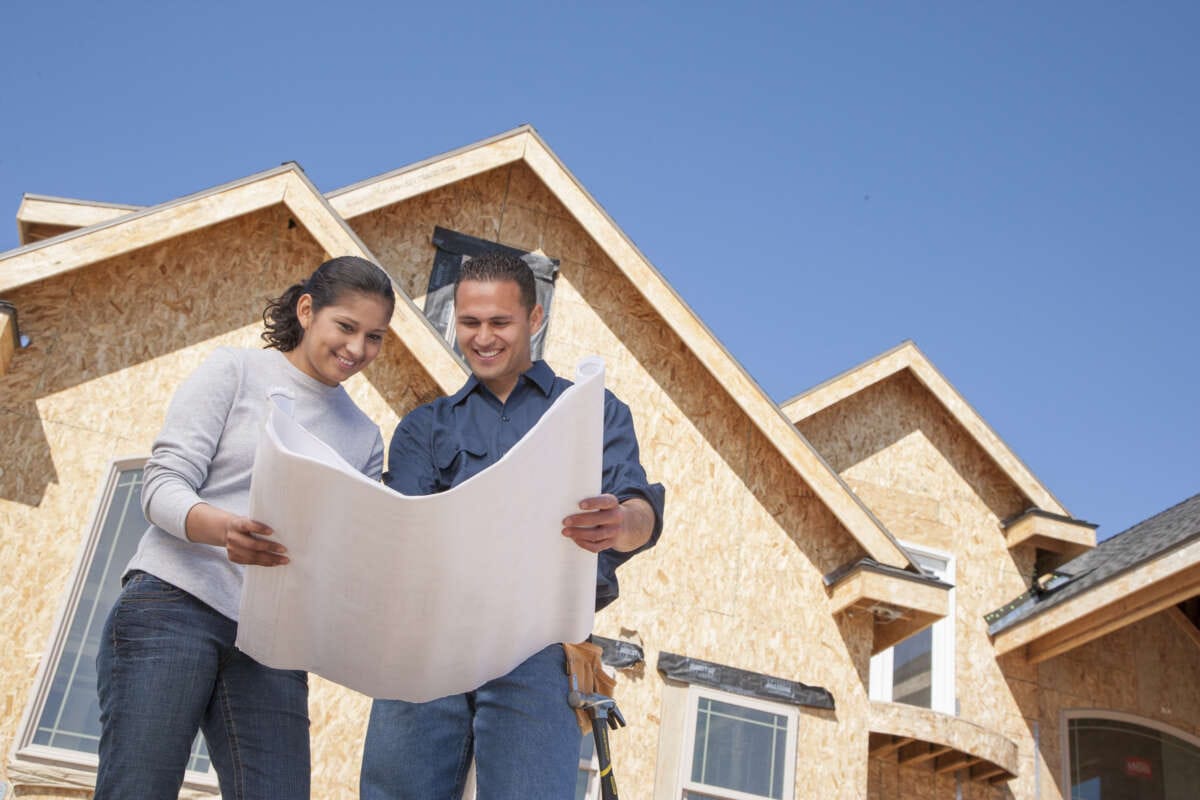
By: Dr Benjamin Coorey-chief executive officer and co-founder of Archistar.
Building a home is a difficult endeavour for any developer, and one could argue an endeavour that has changed very little over the past 30 years. The process still demands a lot of back and forth, as you balance the dreams of your client with the realities of planning rules and construction constraints. In the same 30 years other industries have seen massive digital transformation. You need look no further than the banking and music industries to see what effect digital tools can have on consumers and broader business.
Meanwhile, the process is in a state of flux with the total value of construction work completed in Australia declining by 2.8% year on year in 2020. With the disruption of COVID lockdowns, reducing face to face contact, rising material costs and increased demand for housing, what are the digital tools home builders will look to adopt to stay profitable?
Artificial intelligence
AI in the form of generative design is quickly becoming the industry’s solution to many of the aches and pains of homebuilding. Unlike traditional design, where the process begins with a model based on an engineer’s knowledge, generative design begins with design parameters and uses AI-driven software to generate a range of models within the defined constraints. Tools such as Archistar can generate to a level of detail that would previously require the expertise of town planners and architects. Soil testing, basic airflow and solar modeling that would normally take weeks is auto generated within seconds, reducing costs for development time with some estimating between 30 and 50 per cent. Add to this the ability for these tools to connect with third party resources, homebuilders can even copy and paste pre-designed homes from affiliated partners to test if the design works on a particular site. AI generative design takes the back and forth out of picking a development site and is already being taken up by developers across Australia.
The Internet of Things
More commonly referred to as IoT, The Internet of Things describes the network of physical objects embedded with sensors, software, and other technologies that is used for the purpose of connecting and exchanging data over the Internet.
The implications for homebuilders are huge with 95% of AEC companies surveyed by KPMG saying they believe emerging technologies including IoT will fundamentally change their industry. Where this is predicted to advance efficiency is in materials management. One of, if not the biggest pain of homebuilding is delays in materials due to human error from lack of data. By incorporating sensors and RFID tags on materials we could see automated workflows, allowing developers to see in real time where, when and at what cost materials are arriving on site. We are already seeing IoT being used in large scale construction for concrete curing. Companies such as AOMS Technologies, in Toronto Canada are using the technology to ensure absolute precision while pouring foundations, so it is only a matter of time before similar systems become the norm in Australia.
A constant flow of real-time data from IoT sensors combined with historical data from other projects could not only increase efficiency on current sites but also provide an ever-increasing dataset that, when paired with generative design, could see AEC run even smarter and allow the industry to follow others in data driven decision making.
Factory built and 3D printed
Prefabricated housing is by no means a new concept. The Swedes have mastered the art, with prefab modular housing making up 70% of their construction industry. Our younger market may not be on par with our Scandi friends, but research suggests the sector’s share within the construction industry is forecast to grow from 5% to 15% by 2025, contributing to around 20,000 new jobs and $30 billion of growth.
A prefab revolution in Australia can only bode well for homebuilders and developers. The benefits of factory built homes is consistency, with a controlled environment for work leading to more efficiency in building but also in design properties. Prefab firms are at the forefront of material innovation as they strive for more light weight and thermally efficient building materials to reduce weight during transport.
Arguably what is most exciting to come out of the prefab sector is 3D printing technology. We are already seeing projects come to fruition, like Rancho Mirage led by Might Buildings in California. The development aims to build 15 eco-friendly 3D printed homes on a five-acre parcel of land and be the first in the world to fully integrate the technology into home development. 3D printing may be in its infancy but the benefits of lower labour cost, increased quality control and better control over sustainable practice will make it a desirable process for future homebuilders.
Digital transformation has already swept through a myriad of industries, so it is without doubt that Australian AEC will follow suit. The prospect of a fully digitally integrated homebuilding process from picking the site to fabricating the home, has the ability to dramatically reduce costs and speed up efficiency for developers. Tools like generative design, IoT and 3D printing are already making their mark on today’s construction sites and will only advance the industry’s digital transformation in the years to come.